Innovate UK and Advanced Propulsion Centre competition APC12: “Developing the UK’s long-term capabilities and supply chain in the design, build and manufacture of zero tailpipe emission vehicles”
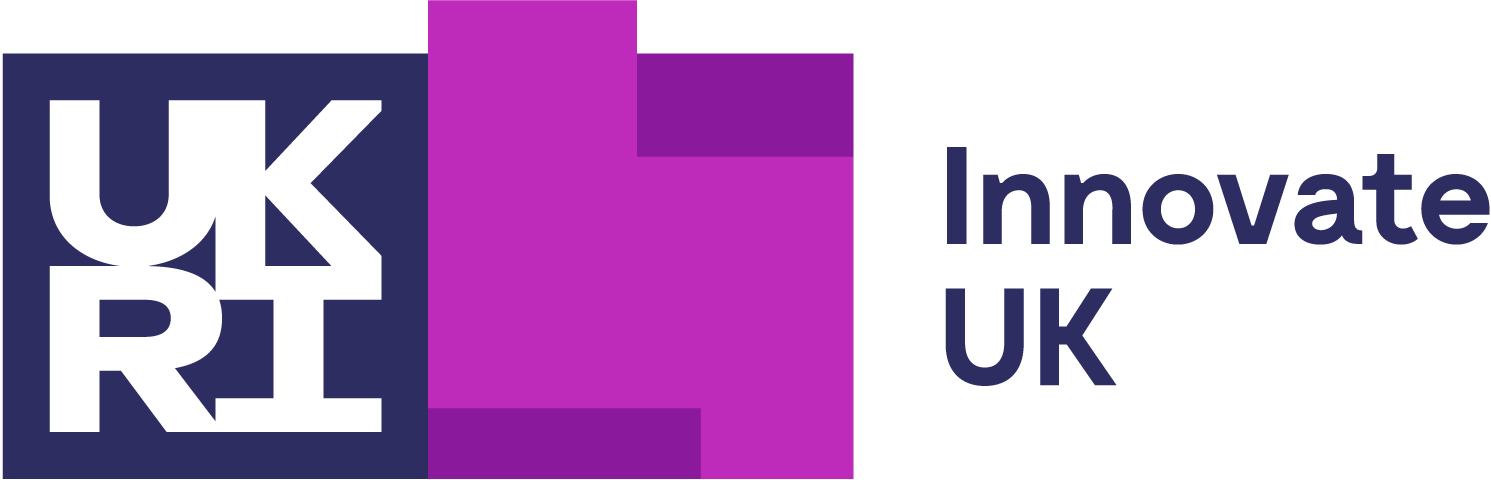

Enabling supply chain collaboration
Hyperbat Limited is a joint venture between Unipart and Williams Advanced Engineering, aiming to become the largest independent battery manufacturer of high-performance battery packs. It relies on disruptive, APC-supported, collaborative research and development (H1PERBAT, APC6).
The H1perChain project, led by Unipart Powertrain Applications, targets the developments and resource growth for Hyperbat to reach critical mass as a commercial scale Tier 1 producer. The H1Perchain project is known as APC12, and it is supported by Innovate UK.
The challenge
Hyperbat has to contend with many-to-many relationships in its supply chain. It’s not just a matter of exchanging data with suppliers on the one hand and customers on the other.
To collaborate effectively, Hyperbat may have to share data with suppliers of suppliers, customers of customers, and other third parties. Moreover, some parties within the supply chain will have direct relationships with each other in addition to their dealings with Hyperbat.
These relationships will only become more complex and data-sharing will become increasingly critical as the joint venture develops.
The challenge is how to avoid ending up with umpteen systems that don’t really communicate with each other, giving users the headache of having to remember numerous logins or forcing people to hunt high and low for the information they need to do their job. And how to keep all the data secure so that each party can easily control what it shares with whom without the risk of inadvertently divulging trade secrets.
Our task was to take a highly mature supplier manual and make it digital, interactive, and auditable, and to automate it to the greatest possible extent – stripping out administrative effort without compromising quality standards.
The goal is to make Hyperbat the EV battery maker of choice: the one that suppliers and customers want to do business with because it’s so easy to innovate and collaborate with them.
The solution
We were fortunate to have a well-defined supplier manual with detailed workflow and processes as our starting point. The manual gave us a clear direction of travel for each piece of data.
This manual provided the framework to create a digital environment and break the work down into clearly defined phases:
- Supplier onboarding
- Design
- Bid process
- Quality
- Supplier feedback
- KPI management
The teams responsible for each phase talk us through how they do their job, what takes time, and what is repetitive and ties them up – so we can understand where to focus our efforts to deliver the optimum outcome.
Through dialogue and regular progress updates we have collectively identified a number of steps that could be automated and therefore remove workload from the highly skilled team. Activities such as chasing NDA status, looking for certifications and accreditations, or searching across existing approved suppliers to engage collaboratively in new opportunities are among the wins identified to date.
The collaboration platform is not seen as a static environment. As the demands on Hyperbat change, so the platform will change with it.
Partner organisations

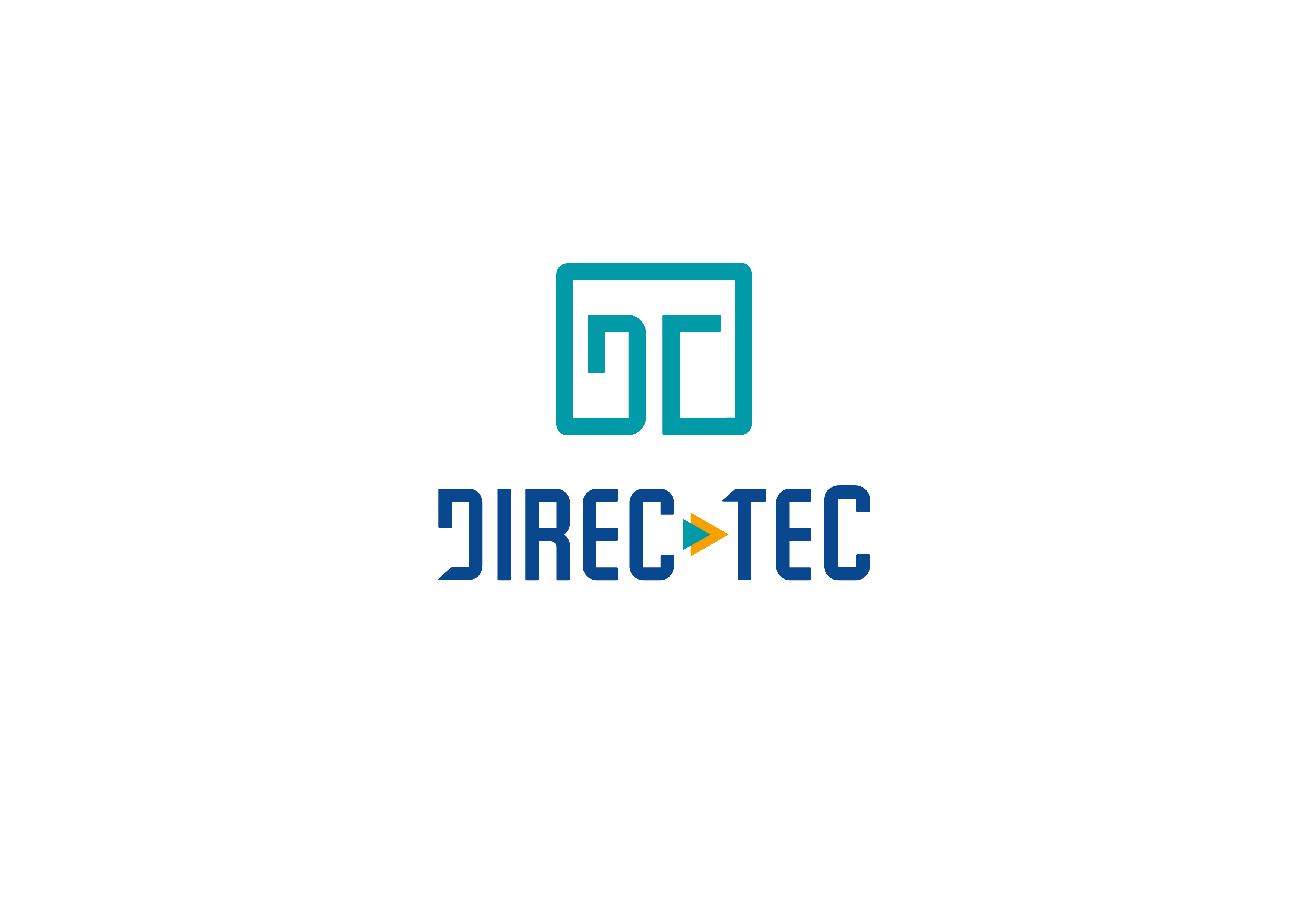
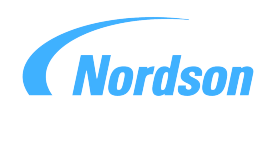
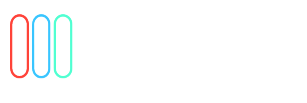
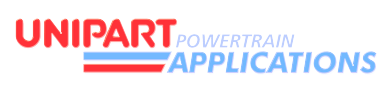
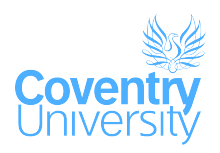
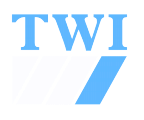
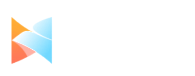