Innovate UK and Advanced Propulsion Centre competition APC12: “Developing the UK’s long-term capabilities and supply chain in the design, build and manufacture of zero tailpipe emission vehicles”
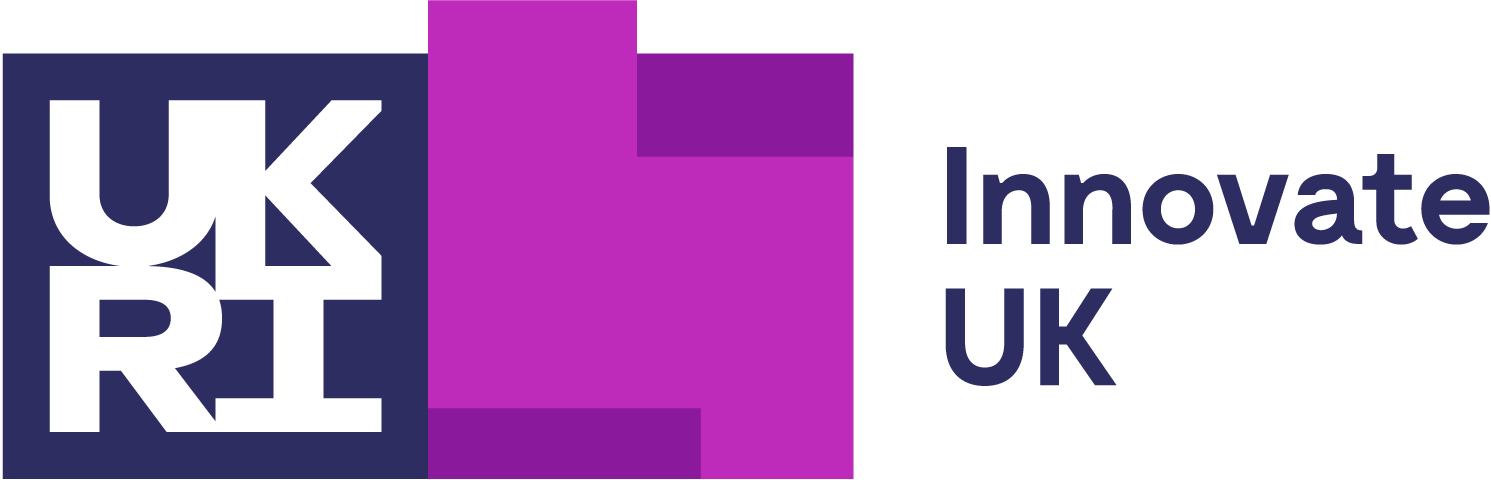

Automating a production line
Hyperbat Limited is a joint venture between Williams Advanced Engineering and Unipart Manufacturing Group.
Hyperbat’s Coventry site opened in 2019 on the site of a former Unipart exhaust plant and is set to produce batteries for future hybrid and electric vehicles, creating about 90 high-value, high-tech jobs.
Hyperbat’s first customer was Aston Martin, which has been using the products in its limited production run Rapide E.
Hyperbat is building a brand-new factory floor, and implementing a new MES (manufacturing execution system) and PLM (product lifecycle management) software.
The challenge
Hyperbat needs a reliable way of connecting the machines on its production line into the MES and PLM software to automate data transmission between production line and business systems.
MES and PLM software is only as good as its ability to integrate with an organisation’s processes, technologies and tools. Hyperbat’s EV (electric vehicle) batteries are a case in point.
An EV battery pack is made up of a number of modules. Each battery module, in turn, is made up of 36 batteries laser-welded into two pieces of metal called busbars: one at the top, one at the bottom. The welds are critical because a great deal of power will run through them during their lifetime and they have to withstand the vibration of a vehicle in motion.
Getting the weld exactly right is the key to the success of a battery. It could mean the difference between a battery that lasts six years and one that lasts two months.
Each individual weld is critical: if the temperature, voltage or power is out, this can result in a fault that might cause the battery to fail or even catch fire. There are thousands of welds in every EV battery pack, and hundreds of data points are captured for each weld to monitor and optimise the weld process.
Hyperbat needs to:
- Collect data from every machine on the production line, such as cobots (collaborative robots) and laser welding machines
- Manage the interaction between the MES and these shop-floor machines
- Map the physical data from machines to the required formats
- Build a central repository that has a view of the entire production line
They also need flexibility so that they can swap out machines without compromising production.
The solution
We engaged with Hyperbat to understand how all these pieces of data fit together, and now Direc-Tec provides the data infrastructure to support a fully automated production line.
In the manufacture process every individual cell is taken off the production line by a cobot and tested before being welded and assembled into a pack while undergoing constant readings and modifications.
We devised the systems that collect the data and send it to the MES. Where the machinery doesn’t speak the same language as the MES, our software translates it for them. This is all part of the solution.
The solution also delivers Hyperbat a version of the data outside of any business system, giving Hyperbat the control of these processes and of the data produced. This helps inform the business in maintaining and improving the quality of its product.
Partner organisations

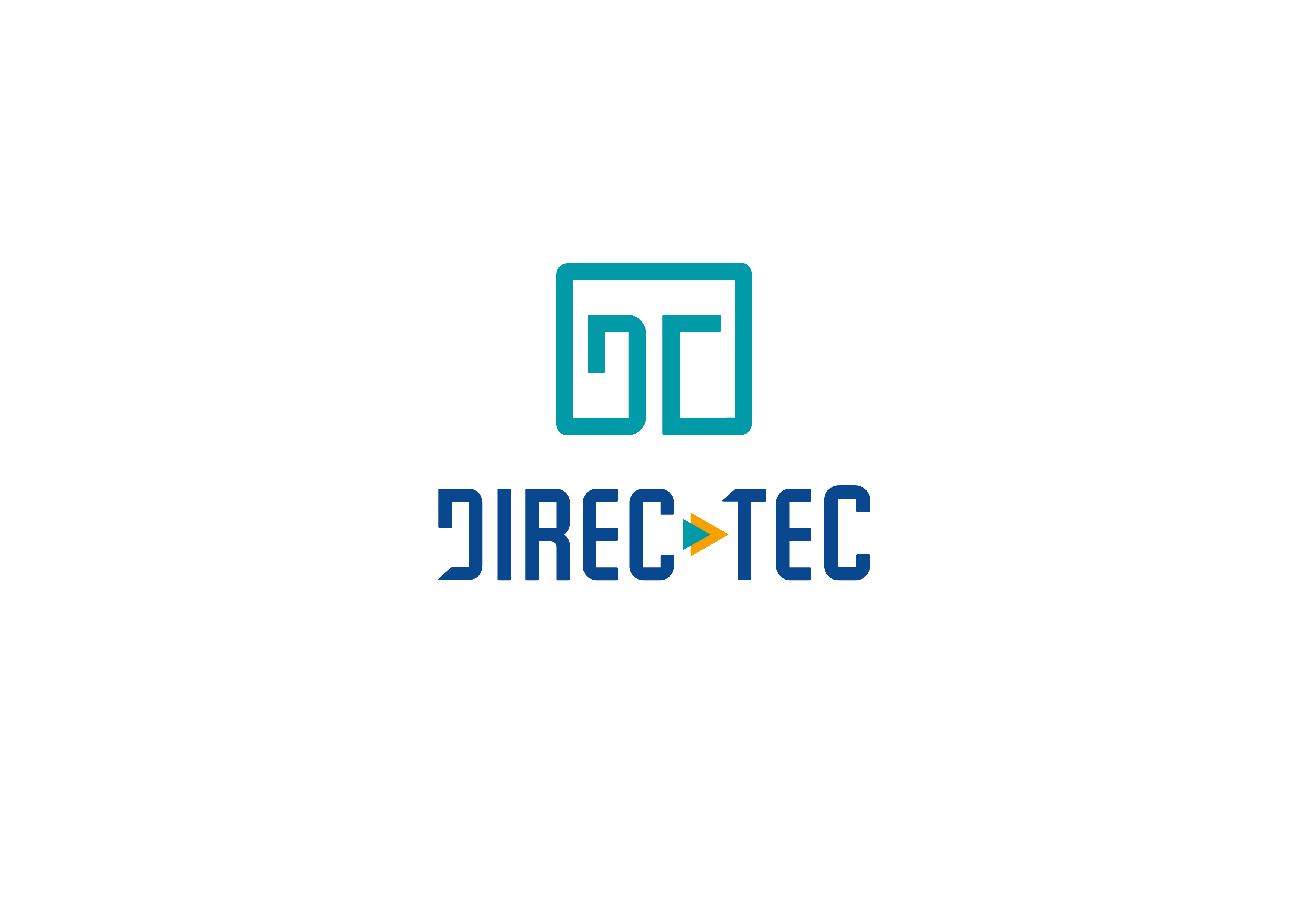
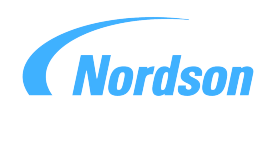
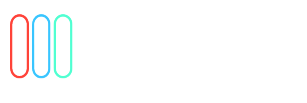
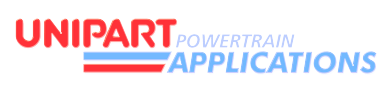
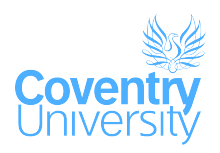
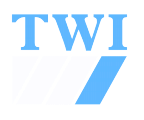
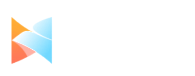